Challenge for the chemical industry
The chemical industry, including petrochemicals, is a top greenhouse gas (GHG) emitter, contributing approximately 20 percent of the world’s GHG total2. Accordingly, Klüber Lubrication has developed KlüberEnergy as a multi-step process to help customers in this sector to increase process efficiency and demonstrate operational energy savings. Steps include Energy Consulting, Energy Measurement, Energy Analysis and Reporting. Savings can be quantified according to ISO 50015 and IPMVP* to support energy management systems (e.g. ISO 50001).
We help our customers to fulfil continuous improvement requirements and meet external targets to become applicants for incentives programs. Compressors, gearboxes, heat transfer systems and exchangers are all considered as applications with energy-saving possibilities. The process results in clear, simple reporting of relevant values, including cost savings, CO2 emissions, ROI, and energy consumption.
Air, gas, and refrigeration compressors are found in many chemical processes, often operating under severe conditions. Poor lubricant choice can directly impact both compressor reliability and efficiency, possibly causing catastrophic failure. With gas compressors, the situation is particularly critical as compressor oils can react with process gases or attack downstream catalysts, causing production issues.
The use of mineral oils in industrial compressor applications is obsolete. Mineral oil is well-known for its poor viscosity vs temperature behavior and low resistance to oxidation. Mineral oil-based lubricants tend to quickly degrade in new technology and high-output compressors. The high operating temperature causes a drastic viscosity drop and premature wear by allowing metal-to-metal friction. Mineral oil degradation will most likely generate varnish and sludge, affecting equipment efficiency.
Klüber Lubrication has a full range of Summit compressor oils, whatever your compressor technology type. Customers suspecting poor efficiency in compressor applications can benefit from the KlüberMonitor oil condition analysis and KlüberEnergy programs to troubleshoot issues.
If varnish or sludge has built up in your screw-type compressor, you can clean it with Klüber Summit Varnasolv and then convert to a Klüber Summit compressor oil for efficiency gains of up to 5 percent.
Chemical industry gearboxes are found within reactor agitators, mixers, extruders, conveyors, grinding mills, centrifuges, cooling towers, bucket elevators, rotary driers/cooler and other rotating equipment. They are designed to transfer power from an electric motor to equipment in motion, and lubrication can directly influence their efficiency.
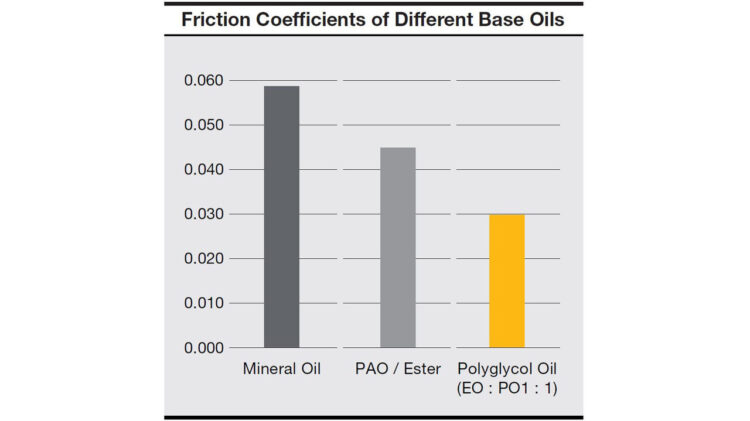
Polyglycols (PAG) based lubricants like our Syngear FG PG Series offer the best energy efficiency, longest service life and highest wear protection. In terms of performance, PAG based lubricants outperform all other synthetic base oils particularly in high-sliding applications such as worm and hypoid gears. Process improvement is possible since the lower coefficient of PAG oils reduces friction within the gearboxes resulting in lower operating temperature and reduced power loss.
Carbon deposits, sludge and varnish present the worst challenges to chemical industry efficiency. Many chemical enterprises still use mineral oils in most of their severe and heavy-duty applications. Pushing mineral oils to their performance and service life limits will most probably lead to varnish and carbon build-up in the entire equipment or circulation system. These sticky residues will cause higher energy consumption, stuck valves, overheating, clogged oil lines and filters, and increased downtime due to maintenance.
Klüber Summit Varnasolv is a concentrated conditioner fluid that acts like a detergent/dispersant to dissolve varnish and carbon deposits during operation in various equipment items, with no dismantling needed. It is miscible with mineral oils, synthetic hydrocarbons, ester oils and polyglycols. The product can also recondition and restore efficiency in oil heat transfer systems that have accumulated a hard deposit, known as fluid coking, on piping inner surfaces. If not eliminated, fluid coking can decrease system heat transfer coefficient, increase energy consumption and exhaust gas temperature, and even block pipelines, inducing fire and explosion hazard.
As many chemical enterprises juggle choices regarding carbon footprint and limited production capacity, they can either add new production lines and pay accordingly, or improve process efficiencies. Sometimes, customers decide to use the improved energy efficiency realized by our specialty lubricants to increase production rather than reduce energy demand.
Whatever your energy efficiency ambition or business objective, you are welcome to contact us for a free technical consultation. Our application knowledge combined with our specialty lubricants is the winning recipe to improve your process efficiency and reliability.
For more information about air compressor lubricants please contact MUSTONLUBE – OFFICIAL DISTRIBUTOR – NY -USA